Investment Units – Technology Deliveries
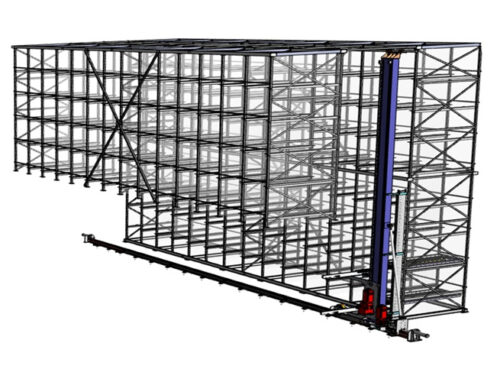
Automatic High Bay Storage
Compas delivers fully automated Hihg Bay Storages (HBS) for storing pallets of materials or products. The stackers can handle hundreds of storage cells in many rows and floors with 1-3 pallets in a row. Full automation of the warehouse is carried out using RFID pallet identification and a continuously updated warehouse database with database records of what is stored in the warehouse.
The warehouse can be supplemented with a real-time factory intralogistics management system (WMS), automatic pallet transport at the input and output (conveyors, AGV/AMR), robots handling goods or a line for packaging and transporting goods to the dispatch.
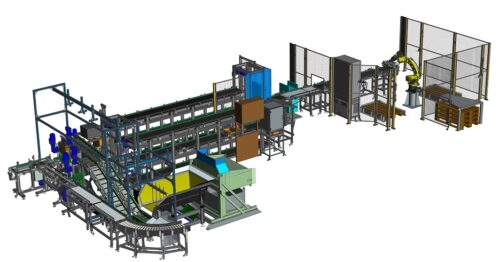
Weighing and Packaging Line
The line is used to package dozens of different types of small metal parts. The parts are poured from the container into the input vibrating hopper, using a system of conveyors and a weighing device, the line divides the parts into KLT or paper boxes. The output package is marked with a label with the exact number of parts. The packages are continuously palletized by a Fanuc robot, which is equipped with a universal gripper so that it can palletize either paper boxes or KLT without operator assistance.
The line replaces the manual work of 9 workers.
Replacement of Manual Labor with Single-Purpose Machines and Equipment
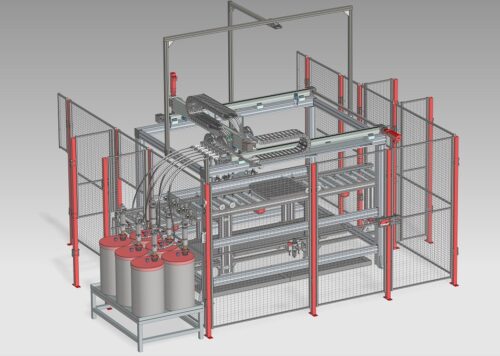
Gearbox Filling Line with Oil
The line is used to fill gearboxes with oil according to a recipe. A gearbox placed on a transport pallet equipped with an RFID chip comes onto the input conveyor, and the conveyor moves the identified gearbox under the dosing head.
The device is equipped with a computer vision camera that finds the gearbox filling hole. The filling heads, placed on a three-axis portal, move over the gearbox opening.
Depending on the gearbox type, the device doses the prescribed amount and type of oil. There are six types of oils to choose.
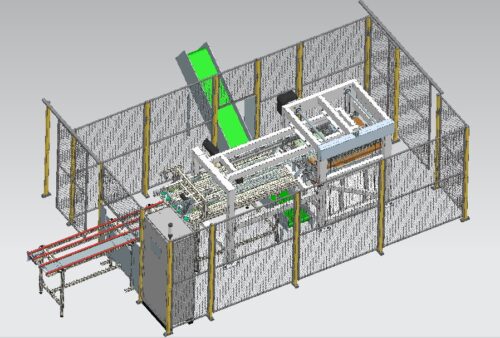
emory Line for Pexeso Separation and Stacking
The Memory line is used to separate perforated edges from pexeso sheets and then stack chopped cardboard strips. The device consists of a pallet loading device, a manipulator with a suction tool, folding conveyors and an output conveyor.
The device’s cycle time allows for the processing of one sheet in 3.5 seconds.
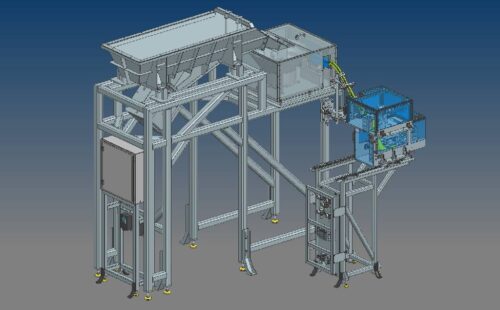
Automated Screw Feeding into NOMOCO Grinder
The machine is used for automatic screws sorting and loading into the Nomoco grinder. The input hopper can hold approximately 450 kg of screws, which are gradually fed into a circular vibrating feeder. Behind the feeder, the screws are directed into chutes and stored in two tracks of a chain conveyor that supplies the grinder. The device is designed for unattended operation. By simple conversion, it is possible to easily switch between different types of screws.
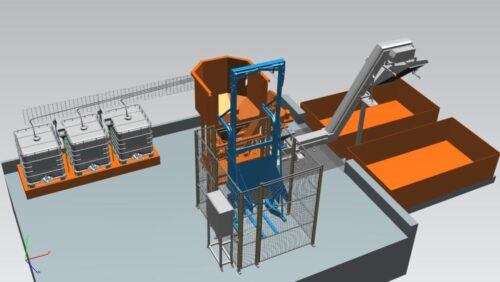
Chip Management Line
The line is used for the separation of oil and metal chips from machining. The equipment automatically tilts the carts with waste material and separates the cutting emulsion and crushes the chips. The chips are automatically sorted into containers according to the barcode and the cutting oil is pumped into one of three IBC containers with level monitoring, depending on the type.
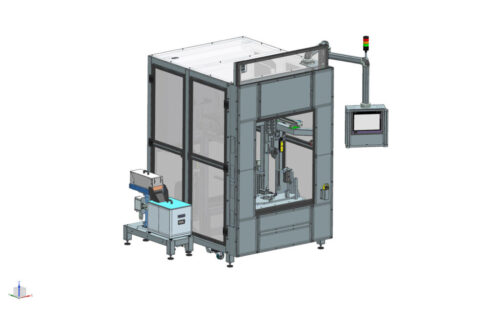
Automated Screwdriving Station
It is used for screwing parts at predefined coordinate points. The station is equipped with two XY gantries and two automatic screwdrivers with position and torque monitoring. It is designed for assembling multiple product types, with the currently loaded type being automatically detected by a camera or sensors. According to the recipe, 10-15 screws of the given product variant are tightened. The station features precise tilting and rotation capabilities, allowing the product to be fully assembled in a single operator setup.
Production Lines for Assembly and Product Completion Using Robots
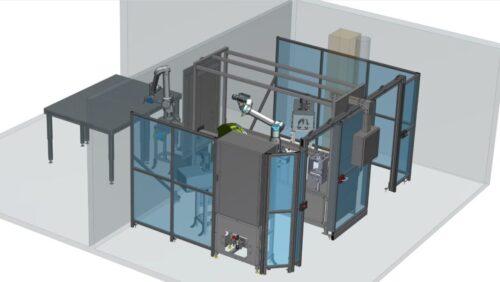
Grinding and Welding with a Cobot
The grinding and welding line consists of two parts, which are structurally separated from each other. In the welding part, automatic welding of aluminum hoops takes place with a laser welding gun. In the grinding part, automatic grinding of aluminum hoops or segments of various sizes takes place. Grinding is performed by a collaborative UR robot, which is equipped with a grinder and an automatic abrasive change function. Tool change is handled by a manually operated tool changer.
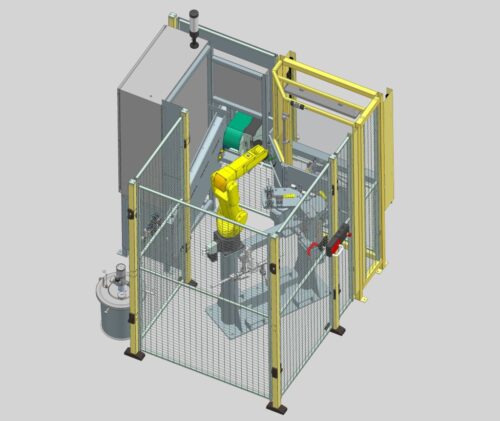
Lubrication and Testing Equipment – WingLine
The WingLine equipment is used to check the completeness of furniture fittings, to lubricate up to 12 given points, to measure the damped movement of the part and the working force of the part. The machine is equipped with a rotating carousel, lubrication and testing is provided by a Fanuc robot, the force is measured by a strain gauge. After lubrication and testing are completed, the machine automatically prints a production label, which the operator manually sticks to the fittings.
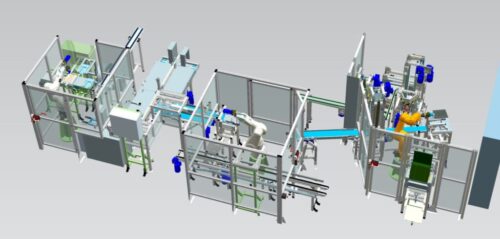
Duction Line with Three Stäubli Robots
According to the customer’s requirements, we developed and delivered a production line with three Staubli robots, which replaced the manual work of three workers in one shift. The line operates in first part in a normal environment, in the other part in an explosion-hazardous environment. We delivered a total of three lines to the customer.
Process Industry
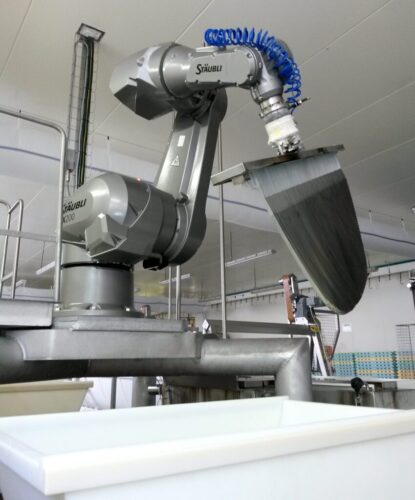
Stäubli Robot Assists in Cheese Production
In the cheese production process, proper maturation requires cutting the curd, which is placed in a plastic tank on the production line. These operations are performed by a robot using two stainless steel sieves, which it automatically switches. The Stäubli robot has replaced heavy manual labor in cheese production.